Chemical industry history
The U.S. chemical industry owed a great debt to Europe, where an inorganic chemical- and coal-based industry, with emphasis on synthetic dyestuffs, started to develop well before it did in this country. The domestic industry came into its own when hydrocarbons from American refineries and natural gas started to be used as feedstock for an organic chemical industry, while Europe’s organic chemicals were still based on coal. World War II gave a further impetus to this so-called petrochemical industry, as North American companies built plants to produce aromatics for high-octane aviation gasoline, synthetic rubber for tires, and a variety of plastics all based on hydrocarbon feedstock. Petrochemical production processes became the growth engine for chemical production throughout the world, with the United States leading in the development and commercialization of many new technologies in this area. As chemical engineering, the science that led to the construction of very large and economical plants, was also pioneered in the United States, the country became the worldwide leader in growing a robust chemical industry. It made synthetic products—polymers and plastics, synthetic rubber, fibers, solvents, adhesives, and many other products—available at relatively low cost to consumers, thus spurring rapid growth of the industry as natural materials—wood, cellulose, glass, paper, metals—were increasingly replaced by synthetics.
Europe and Japan built a similar petrochemical industry, often based on U.S. technologies. Later, other regions and countries started to build plants of this kind, a trend that accelerated as a number of countries in the Middle East and elsewhere started to industrialize, in some cases based on inexpensive local hydrocarbons from crude oil and natural gas. The U.S. chemical industry, which had undergone an unprecedented wave of innovation, development, and growth between 1940 and 1970, entered a more mature phase by the 1980s, when technology development slowed and international competition started to become a factor.
Many petrochemical processes had started to reach the limit of further improvement, and so researchers turned their attention increasingly to pharmatechnology and biotechnology, to electronic chemicals for computers and other hightech equipment, and to other such specialties, which had greater potential for profit. At the millennium, the U.S. chemical industry was in intense competition with many other countries and had largely lost the advantages it had originally enjoyed due to low-cost feedstocks available on the U.S. Gulf Coast. The industry is now considered largely mature, in a manner similar to that of the cement, steel, and paper industries, but it has remained one of the biggest and most important domestic industries.
The domestic chemical industry can be said to have started in the Philadelphia area when DUPONT DE NEMOURS built its first black powder plant in 1802, followed a couple of decades later by a sulfuric acid plant built in Bridesburg. In Baltimore shortly thereafter, a superphosphate plant was built, which treated bones with acid. In 1839, Eugene Grasselli, an Italian immigrant, built a lead chamber sulfuric acid plant. Tar distilleries, based on coal tar from coke ovens, started being constructed later in the 19th century, separating from tar wastes and off-gases a number of organic chemicals, such as benzene, phenol, creosotes, naphthalene, and higher aromatic chemicals, as well as ammonia. Coal-based town gas for household uses also started being produced, yielding similar materials as chemical byproducts. The Solvay process for the production of soda ash, developed in Europe, was placed into production near Syracuse, New York, in 1884, and two other plants of this kind were built at the turn of the century to supply the new plate glass industry. A Canadian, T. L. Willson, built an electric furnace to make calcium carbide, leading to the production of acetylene and calcium cyanamide in North America in 1905, a notable producer being American Cyanamid.
Europe’s chemical industry led that of the United States in a number of ways, based on a traditionally greater emphasis on chemical research in Germany, France, England, and other countries. In the late 1700s and 1800s, researchers such as Lavoisier, Berthelot, Gay-Lussac, Kekule, Sabatier, Woehler, Liebig, Perkin, Nobel, and others made many breakthrough developments that led to the establishment of plants to produce synthetic dyestuffs, human-made fibers, explosives, soda ash, solvents, and medicines, such as acetylsalicylic acid (aspirin). Synthetic dyestuffs such as alizarin and indigo, to supplant and eventually replace imported natural dyes, began production in England, Germany, and France in the 1860s and 1870s using raw materials from coal distilleries. The German chemical industry in particular became paramount not only in its own market but also in exporting to other countries including the United States. Eventually the I. G. Farben CARTEL became so powerful that it dominated world production in many chemicals, as it also established plants, joint ventures, or other cooperative arrangements (such as selling cartels) with U.S. producers DuPont, Allied Chemical, and others. The development of dynamite production by Alfred Nobel, based on nitroglycerine, led to another worldwide cartel, which included two plants in the United States by 1873.
Nitric acid was first produced by the Merrimac Chemical Company in 1905 and aniline by the Benzol Products Company in 1912. Synthetic phenol via the chlorobenzol process was made by DOW CHEMICAL shortly after World War I, taking over from a less efficient phenol process.
The first plastics developed in England were based on nitrocellulose and camphor and known as Xylonite. In the United States, John Wesley Hyatt, looking for a substitute for the ivory used in billiard balls, established a plant in Newark, New Jersey, to make this type of polymer in 1872, giving it the name Celluloid. It was soon used to make knife handles, films, collars and cuffs, and other products. It became the most important plastic produced until 1909, when Leo Baekeland, a native Belgian who had immigrated to the United States, discovered another plastic material based on phenol-formaldehyde, which was termed Bakelite.
Monsanto had been established in 1902, first as a producer of saccharin, then of other organic and inorganic chemicals. Cellulose was also initially used to produce so-called manmade fibers and films. Cellulose acetate, first produced in France, did not become commercially important until acetone could be used as a solvent, leading to so-called acetate silk, manufactured in the United States and elsewhere around the turn of the century. The first highly successful manmade fiber, viscose rayon, based on wood or cotton pulp, was developed by Courtaulds in England in 1895 and was first produced in the United States by Avtex Fibers in 1910.
By 1914, the U.S. chemical industry had become relatively self-sufficient, with the exception of having to import potash and nitrates, as well as having essentially no dyestuffs industry. Chlor-alkalies were being produced in quantity at Niagara Falls and elsewhere, with Hooker Chemical, Niagara Alkali, and Dow as important producers. The Frasch sulfur mining process developed on the Gulf Coast, where large deposits had been discovered, started to yield large quantities of sulfur for sulfuric acid production and other sulfur compounds. Borates were produced by U.S. Borax in the West. Stauffer Chemical was making acids and phosphates, and a British firm, Albright and Wilson, was producing phosphorus and sodium chlorate. Industrial gases were produced by Air Reduction Company, affiliated with Air Liquide in France, and by Linde Air Products Company.
Union Carbide and Chemicals acquired the Presto-Lite company, which had for some time produced acetylene from calcium carbide for use in automobile headlights and street lights. Union Carbide also bought an interest in Linde and started experimenting at Linde’s plant in Tonawanda, New York, to crack hydrocarbons in order to make both acetylene and ethylene from ethane, plentiful in natural gas. A commercial plant was built near Charleston, West Virginia, in 1921, and by 1927, the firm was making ethylene glycol for a product needed in antifreeze protection for automobiles. In 1923, Ethyl Corporation introduced tetraethyl lead to raise gasoline octane, making possible the development of high-compression car engines.
High-pressure synthesis work in Germany just before the war was responsible for one of the biggest chemical industry breakthroughs, the development of a process to make synthetic ammonia from hydrogen and nitrogen. While the process was patented and therefore not readily available to U.S. companies, within a decade Shell Chemical in Martinez, California, and DuPont at Belle, West Virginia, were able to build synthetic ammonia plants with successful operations achieved in 1930, using a somewhat lower pressure to skirt the BASF patents.
Dow Chemical, incorporated in 1892, had become a large producer of bromine from wells in the Midland, Michigan, area. A joint venture with Ethyl Corporation at Kure Beach, North Carolina, used a process to extract and purify bromine from seawater. In the late 1930s, Dow built the first large-scale outdoor chemical complex on the Texas Gulf Coast to extract bromine and magnesium from seawater, also making chlorine- caustic, ethylene, ethylene glycol, and ethylene dibromide, used as a solvent for tetraethyl lead (TEL).
Thermal cracking plants installed by refineries were yielding increasing quantities of ethylene, propylene, and aromatics, all ideally suited as petrochemical feedstocks. The first so-called petrochemical plant was built by Esso (now Exxon) at the Bayway, New Jersey, refinery, making isopropyl alcohol via the hydrolysis of refinery propylene, using sulfuric acid to effect the reaction. Esso at that time had strong relations with Germany’s I. G. Farben combine, whereby the know-how for a number of technologies developed by the two entities was shared. For example, the German firm provided to Esso its know-how in hydrogenation reactions, while Esso shared its knowledge of making TEL. In the late 1930s, Esso started high-temperature steam cracking of crude oil fractions to ethylene and higher olefins, related to the work that Union Carbide had been doing in Charleston. Hydrogenation was used to remove sulfur from refinery streams going into gasoline and fuel oils.
Shell Chemical at its Emeryville, California, research laboratories was developing techniques to make high-octane blending components (e.g., isooctane) from propylene and butylenes using a dimerization catalyst. Other developments commercialized by Shell in the 1930s included synthetic glycerin and methyl ethyl ketone, which became an important paint solvent.
The 1930s also saw considerable progress in the field of plastics. Union Carbide and B.F. GOODRICH developed techniques to soften polyvinyl chloride (PVC) resin, the product formed by copolymerization with vinyl acetate, the latter by the development of so-called plasticizers. PVC became the first important thermoplastic resin, finding a myriad of uses in piping, seat covers, shower curtains, toys, and other applications. Meanwhile, Dow was working on technology to produce styrene, leading a few years later to production of polystyrene resins, which have much greater clarity than PVC. Dow polystyrene was put on the market in 1937.
The much-heralded work by Wallace Carothers at DuPont led in the late 1930s to the development and commercialization of a number of synthetic polymers and fibers, notably nylon. Somewhat earlier, DuPont had built a plant to make neoprene, a specialty rubber. Teflon, an inert plastic with many uses, was also developed by DuPont around the same time.
An important shift in plant design saw the construction of chemical plants in open-air sites, starting on the U.S. Gulf Coast at such places as Freeport, Texas (Dow), Texas City (Union Carbide, Monsanto), Baton Rouge (Esso, Ethyl Corporation), Orange (DuPont), and Lake Charles (PPG, Conoco). Previously, following European tradition, plants had generally been built inside buildings.
The 1930s also saw the end of U.S. chemical companies’ participation in several cartels that had their origin in Europe. The Justice Department and the FEDERAL TRADE COMMISSION attacked these cartels as being monopolistic and in restraint of trade. Only export cartels, as allowed under the Webb-Pomerine Act, were allowed from that point forward.
The Second World War was a crucible for the North American chemical industry, as it became one of the most essential industries supporting the war effort. With imports of natural rubber from Japanese-controlled Malaysia no longer possible, several domestic companies developed synthetic rubbers for tire and hose production based on styrene, butadiene, and acrylonitrile. Some of this technology had also come from Esso’s exchange of technical information with I. G. Farben.
Work on dimerization, dehydrogenation, and aromatization of hydrocarbon fractions produced massive amounts of high-octane blending components for aviation and automobile gasoline. Fighter planes in particular required high-octane for rapid takeoffs. A number of synthetic polymers and fibers were produced in increasing quantities, including nylon for parachutes, polyethylene for radar equipment, specialty solvents, and many other “petrochemicals.” Antibiotics, more powerful than the sulfa drugs then in use, were developed during this period, with production of penicillin by Merck, Pfizer, Squibb, and Commercial Solvents Corporation, among others.
The Manhattan Project, which in 1945 resulted in the capitulation of Japan due to the bombs dropped on Hiroshima and Nagasaki, was one of the most significant achievements, as chemical engineers learned how to separate and concentrate uranium isotopes to produce fissionable materials.
The end of the war, with its shortages of consumer products and an even longer pent-up demand as a result of the Great Depression, brought about an unprecedented buying wave in durable goods such as housing, automobiles, and appliances. With synthetic materials becoming broadly available to factories that shifted their output from war materials to consumer goods, petrochemicals started a period of “double digit” growth that lasted until the late 1960s. Now, a number of companies wanted to make petrochemicals, which were rapidly replacing, in many applications, such conventional materials as glass, wood, natural rubber, iron, copper, aluminum, and paper. A number of old-line companies making these traditional materials (e.g., U.S. STEEL, Goodyear, B.F. Goodrich, Georgia Pacific, Pittsburgh Plate Glass) and others now entered the manufacture of petrochemicals, using technologies licensed from engineering firms and competing with the traditional chemical companies that were loath to let in these newcomers. Most of the oil companies now also established a petrochemical division. By the end of the 1960s, sales of several petrochemicals were measured in billions of pounds per year.
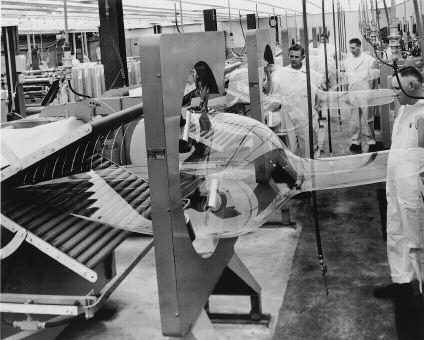
The 1960s and 1970s saw a rapid increase in the internationalization of the chemical industry. German, French, British, and Dutch firms made a number of acquisitions and joint ventures in the United States, such as Wyandotte Chemical by BASF; Mobay, a joint venture between Monsanto and Bayer; ICI’s acquisition of Atlas Chemical; and DSM’s majority investment in the fiber company American Enka. Belgium’s Solvay established a U.S. subsidiary. Conversely, such firms as Dow Chemical, Union Carbide, DuPont, Gulf Oil Chemicals, Esso Chemical, National Distillers and Chemicals, and Monsanto invested in Europe, generally building plants for which exports had previously established good markets.
This was also a period when chemical producers recognized the economic advantage of scale and started to build much larger (“single train”) plants than had been built to date. In ethylene, ammonia, styrene, and several other products, these large plants, which were made possible by a number of chemical engineering process and equipment breakthroughs, established new economics for the MASS PRODUCTION of these chemicals.
A pattern of consumption of chemicals was being established, and it continues to the present time. Highest production inorganics were sulfuric acid, ammonia, chlorine, caustic, phosphoric acid, hydrogen, oxygen, and nitrogen gas. Highest production organics were ethylene, propylene, ethylene dichloride, benzene, urea, and styrene. Plastics and resins included polyethylene (several densities), polypropylene, PVC, and polystyrene. Synthetic fibers were led by polyester, nylon, and olefin.
This period also saw the establishment and/or rapid growth of a number of specialty chemicals manufacturers, such as W. R. Grace, Hercules, Nalco, Petrolite, Witco, National Starch and Chemicals, and many others. These firms, generally using less complicated technologies, made various types of chemicals (e.g., adhesives, sealants, water treating chemicals, photographic chemicals, mining chemicals, personal care chemicals) that facilitated production processes or imparted special characteristics to consumer products. Fine chemicals were also produced in large quantities, in many cases as feedstocks for a rapidly growing PHARMACEUTICAL INDUSTRY, including such firms as Pfizer, Merck, Smith Kline, Wyeth Laboratories, Eli Lilly, and American Home Products.
The first oil shock in 1973 and the second in 1978–79 became landmark events for the domestic chemical industry. It soon became clear that the industry could no longer depend on very cheap, copiously available hydrocarbon feedstocks to produce petrochemicals. From a pre- 1973 price of $3 per barrel, crude oil prices rose as high as $30 per barrel in 1979, eventually settling between $15 and $25 per barrel in the 1980s and 1990s. Natural gas, which had cost as little as 15 cents per million BTU, rose to a level between $2 and $2.50, following the higher crude oil prices as well as higher production costs and diminishing sources of low-cost gas.
Important changes were taking place as the U.S. chemical industry faced increasing maturity, with demand growth for its products dropping from a double-digit rate to less than twice the GDP growth and with technology innovation at a much lower level. Meanwhile, a number of countries in the developing regions of the world (Korea, Thailand, Malaysia, Taiwan, Brazil, and Saudi Arabia) were rapidly building up an internal chemical industry, either to supply local markets or for exports or both. Inexpensive hydrocarbon deposits in western Canada, the Middle East, and several other areas provided the basis for large export-oriented plants, which started to compete strongly with the once heavily advantaged U.S. petrochemical plants on the Gulf Coast. By the end of the century, the balance of trade in chemicals, once highly positive and amounting to more than $20 billion of exports over imports, had actually become negative.
A tremendous amount of industry restructuring and, to a lesser extent, consolidation took place in the 1980s and 1990s, as companies had to decide whether to stay in or to quit the production of highly competitive petrochemicals and whether to shift much of their portfolios to the production of higher-value specialties. Many old-line chemical companies (Stauffer, Allied Chemical, National Distillers, etc.) disappeared due to MERGERS and acquisitions, and a number of oil companies decided to sell or exit their petrochemical operations.
The chemical industry had also become a target of environmentalists, who pointed to the hazardous nature of its operations and the exposure of workers and the public to toxic chemicals. The industry became highly regulated at the federal, state, and local levels and was spending a large part of its cash flow on meeting environmental standards and on chemical testing.
Once the darling of the investing public due to its rapid growth and the miracles of technology that have been responsible for a plethora of new synthetic materials, the chemical industry has become increasingly embattled as it tries to operate in a manner to satisfy its various stakeholders. With exports declining due to foreign competition, and some products voluntarily phased out due to their toxic characteristics, it has remained one of the largest domestic industries, essential to our standard of living, yet increasingly on the defensive and unsure of its future.
See also PETROLEUM INDUSTRY.
Further reading
- Aftalion, Fred. A History of the International Chemical Industry. Philadelphia: Chemical Heritage Press, 2001.
- Barnes, Harry C. From Molasses to the Moon. The Story of U.S. Industrial Chemicals Company. New York: U.S. Industrial Chemicals Company, 1975.
- Borkin, Joseph. The Crime and Punishment of I.G. Farben. New York: Macmillan/Free Press, 1978.
- Brandt, E. N. Growth Company. Dow Chemical’s First Century. East Lansing: Michigan State University Press, 1997.
- Chapman, Keith. The International Petrochemical Industry. Oxford: Basil Blackwell, 1991.
- Spitz, Peter H. Petrochemicals. The Rise of an Industry. New York: John Wiley & Sons, 1988.
- ———. The Chemical Industry at the Millennium. Philadelphia: Chemical Heritage Press, 2003.
Peter Spitz
Tweet